Posts Tagged ‘Supply-Chain Management’
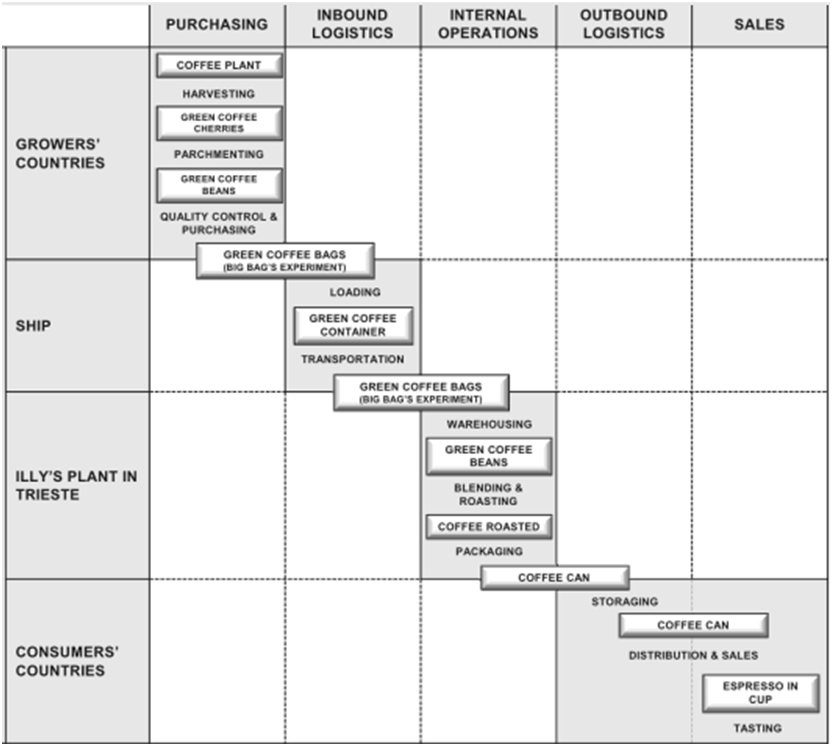
Illy is a global coffee brand that is sold in 140 countries and employs more than 800 people globally (Illy: By the Numbers, 2013). The main difference between traditional logistics and supply chain has been drawn by Agrawal and Smith (2009) in a way that supply chain is a much broader concept than logistics and it focuses on the quality of relationships between various elements within the supply chain with the aims of achieving improvements Elements of supply-chain management (SCM) have been specified by Wisner et al. (2008) as purchasing, operations, distribution, and integration. Wisner (2008) argues that effectiveness in one particular element does not compensate shortcomings in other elements, and thus businesses need to strive to strive to obtain competitive advantages each of these elements. Three major tendencies impacting SCM have been specified by (Muller, 2011). Firstly, increasing numbers of businesses are acquiring their resources from other countries. Secondly, timeframe associated with the delivery of resources and the quality of resources is playing increasing role for firms in terms of obtaining competitive advantage. Thirdly, rapid technological developments among a range of other factors are causing uncertainties in the market with direct implication on SCM practices Ruston et al. (2010) advocate the adoption of strategic approach in dealing with suppliers. This viewpoint has been supported by a wide range of other authors as well, and the benefits of adopting a strategic approach with suppliers have been listed as more effective quality control based on trust (Leeman, 2010) and achieving greater level of supplier cooperation in times of economic difficulties (Agrawal and Smith, 2009). Basu and Wright (2012) further expand this point and argue that adoption of strategic approach in dealing with suppliers based on ethical practices can have highly positive implications on business brand image if these relationships are communicated…
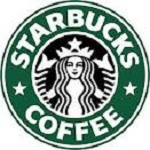
Value network analysis can be applied in relation to Starbucks operations in the UK in order to “explore the structure of its interaction with several actors in a network of relationships” (Zsidisin and Ritchie, 2008, p.40). In simple terms, value network analysis can be specified as more sophisticated version of Porter’s Value Chain analysis in a way that the former framework explains the impact of each network group in a multidirectional manner. For example, as it is illustrated in the following figure, media as an important network group within Starbucks value network has direct implications on the performance of three other individual network groups: suppliers, company operated stores, and licensed stores. This specific interrelationship can not be effectively presented within Porter’s value chain network, due to the fact that this framework is constructed in a rigid and sequential manner. The following table briefly explains the nature of impact each individual network group within Starbucks value network Network group Comments Company operated stores The largest source of revenues from the sale of drink and food products Licensed stores Licensed stores contributed to 9% of total revenues during the financial year of 2011 (Annual Report, 2011). Suppliers This network group comprises suppliers of coffee beans, food products, and various tools and technologies.Suppliers are used by Starbucks for company operated stores, whereas, licensed stores deal with their suppliers in a direct manner. Farmer Support Centres are maintained in Rwanda, Costa Rica and other locations UK Government agencies UK government agencies as an independent network group can impact both, company operated stores, as well as, licensed stores Media Has great impact on the performance of both, company operated and licensed stores. Recently, this impact has been highly negative due to extensive coverage of tax issues from a critical viewpoint.Unlike other network groups, media…
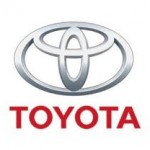
Supply-chain management at Toyota is an element of company’s operations strategy which is thoroughly based on the Toyota Production System (TPS). It was developed in the 1940’s by Shigeo Shingo and Taiichi Ohno. As Toyota’s success gained world-wide coverage, at was followed by interest by other companies in TPS, the principles of which is expressed by the term of “lean manufacturing” Liker (2005, p.16) lists following components of Toyota Supplier Partnering Hierarchy: mutual understanding and trust, interlocking structures, control systems, compatible capabilities, information sharing, joint improvement activities, and Kaizen and learning. “JIT system – a system that organizes the resources information flows and decision rules that enable a firm to realise the benefits of JIT principles”. (Krajewski, Ritzman & Malhotra p.349) The elements of just-in-time system are being pro-active in exposing problems, pull production based in Kanban, Total Quality Management, elimination of waste, reducing inventory through involving suppliers in planning process, continuous improvement, improving machinery and focusing on co-operation. According to Kanban each part travels with a card. New stock will only be required when that part has been used, the card is removed, using signals to re-stock this part. Kanban is well integrated in Toyota’s production system, because in Toyota there are limited number of parts with stable demand for them. Also, product mix is low and exchanges are infrequent. Capacity planning in any company is part of a supply-chain management for that specific company. Toyota’s way to capacity planning is that it strives to eliminate inventory. In achieving this objective Toyota relies heavily in pull system. Generally, the main objective is continuous improvement. Another operational excellence pioneered in Toyota and later adopted by other companies worldwide is a “Lean Concept”. Lean philosophy aims to achieve are the elimination of all waste, superior customer care, and Lean is based…
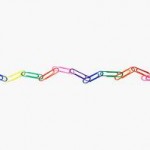
Defining logistics and quality within supply chain management Supply chain management. According to Wilton (2005, p.22 ), the term logistics has originated around 1930’s from the French word “logistique”, which is taken from the word “loger” meaning dividing troops. Nowadays, the term logistics is used in different spheres, bearing different meanings. The Council of Supply Chain Management Professionals (CSCMP) define logistics as “the plans, implements and controls that effectively and efficiently forward and reverse the flow and storage of goods, services and related information between the point of origin and the point of consumption in order to meet customer’s requirements”(CSCMP – online, 2010). Alternative definition of logistics is provided by Webster’s dictionary as “the procurement, maintenance, distribution, and replacement of personnel and material”(Webster’s Dictionary – online, 2010) Mentzer et al. define supply chain as a “set of three or more entities (organizations or individuals) directly involved in the upstream and downstream flows of products, services, finances, and/or information from a source to a customer” (2001, p.4) The quality within supply chain management is defined by the author of present essay as the measure of supply chain in terms of reducing costs of supply chain and increasing its efficiency. Houlinah (1998, p.14) lists the following differences between supply chain management and traditional manufacturing materials control. Firstly, supply chain is seen as a single process. Second, supply chain requires strategic approach and decisions making. Third, supply chain requires a different approach to inventory. And, fourth supply chain requires integration rather than interfacing for system approach. The objective of managing supply-chain, according to Stevens (1989, p.5), is to synchronise the requirements of the customer with the flow of materials from suppliers with the aim of effecting the balance to achieve high customer service, low inventory management and low unit cost. Companies in any…