Value-Chain Analysis
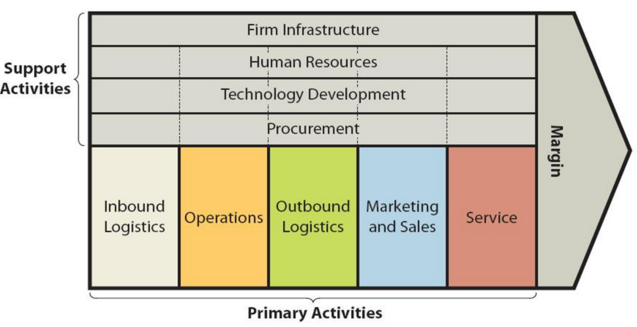
Value chain analysis is a strategic analytical tool that can be used to identify business activities that create the most value. The framework divides business activities into two categories – primary and support. The figure below illustrates the essence of Square value chain analysis. Square Value Chain Analysis Square Primary Activities Square Inbound logistics Inbound logistics refers to receiving and storing raw materials for their consequent usage in producing products and providing services. Along with a wide range of financial services, Square offers related hardware products such as card readers, stands, terminals, registers, hardware kits and accessories. The majority of hardware products are produced in China. Accordingly, cost-effectiveness of producing hardware products is the main source of value creation in inbound logistics for Square. Square Operations Square operations are divided into the following two segments: 1. Seller ecosystem. An expanding ecosystem of products and services that are designed to assist sellers to start, run and grow their businesses. In 2019 this segment processed USD106.2 billion of Gross Payment Volume (GPV), which was generated by nearly 2.3 billion card payments from 407 million payment cards.[1] 2. Cash ecosystem. This segment centred on Cash App integrates financial products and services that help individuals manage their money. As of December 2019, Cash App had approximately 24 million monthly active customers who had at least one transaction in any given month.[2] The main source of value creation in operations primary activity for Square refers to high level of speed and convenience of products and services enabled by technology. The finance sector disruptor spotted demand in both segments and developed products and services to satisfy demand with the use of the latest technology. Square Outbound Logistics Outbound logistics involve warehousing and distribution of products. Square uses the following distribution channels to distribute…
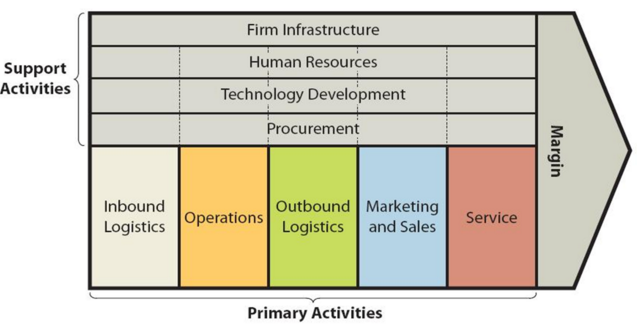
Uber Value chain analysis is a strategic analytical tool that helps to identify the sources of value and competitive advantage for the global transportation technology company. Figure below illustrates the essence of Uber value chain analysis. Uber Value Chain Analysis Uber Primary Activities Uber Inbound logistics Generally, inbound logistics involves receiving and storing raw materials. Uber, the largest taxi technology company in the world, does not own the vehicles it uses to serve customers. The vehicles are owned or rented by Uber drivers, who are not employees, but independent contractors. Uber drivers need to possess smartphones to use Uber app software. Uber users, i.e. customers also must have access to a smartphone or mobile website to be able to use the service. Accordingly, value addition in Uber inbound logistics relates to internet-based nature of business operations and the business model of the company. Specifically, thanks to its business model, despite the large size of the business, Uber inbound logistics is only limited to mainly hardware and office equipment needed to sustain the business. The global transportation technology company does not need to procure any raw material for provide its services. Uber Operations Uber operations are highly sophisticated and customer-centric thanks to its app equipped with advanced functions and capabilities. Therefore, it can be argued that Uber app is one of the main sources of value in Uber operations. Uber operates in approximately 10000 cities worldwide. Business operations are divided into four reportable segments: 1. Mobility. In Mobility segment Uber operations consist of connecting consumers with independent providers of ride services. The usage of Uber mobility services involves the following stages: a) Requesting the ride. Customers can use Uber app to tap each ride option to see wait time, driver’s rating, and price. Customers can enter their pickup location and…
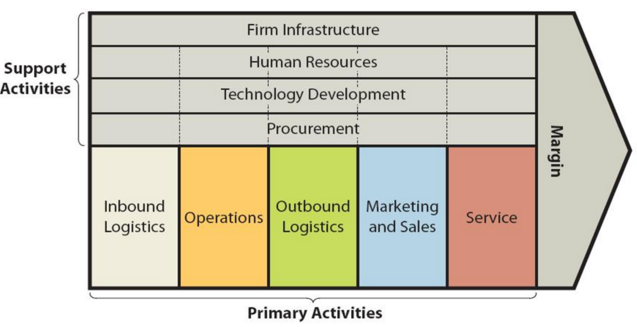
Tesla value chain analysis is an analytical framework that assists in identifying business activities that can create value and competitive advantage to the electric automaker. Figure below illustrates the essence of Tesla value chain analysis. Tesla value chain analysis Primary Activities in Tesla Value Chain Analysis Tesla Inbound logistics Tesla inbound logistics involves the receipt and storage of raw materials to build electric vehicles, energy storage systems and solar panels. Along with a standard set of raw materials, Tesla uses a range of scarce materials such as aluminium, steel, cobalt, lithium, nickel and copper. In the US, the company receives parts at its Fremont automotive factory from thousands of suppliers worldwide, including from its very own Gigafactory in Sparks, Nevada. The electric automaker leases three warehouses totalling a massive 1.3 million square feet in the Oaks Logistics Centre in Livermore, California., just 20 miles northeast of the Fremont factory as a storage for raw materials. Additionally, in 2019, Tesla constructed 870,000-square-foot facility in Lathrop, California as a massive spare parts storage.[1] Currently, highly sophisticated inbound logistics practices are not one of the main sources of value creation for the electric automaker. Tesla works primarily on a build-to-order basis, which means bottlenecks in parts supply could be a big headache.[2] Accordingly, it is critically important for Tesla to establish long-term strategic relationships with suppliers. Tesla Operations Tesla conducts vehicle manufacturing and assembly operations at its facilities in Fremont, California; Lathrop, California; Tilburg, Netherlands and Shanhhai, China. Generally, Tesla operations can be divided into two segments: 1. Automotive. This segment comprises design, development, manufacturing, and sales of electric vehicles. The company produced and delivered approximately half a million vehicles in 2020.[3] The electric automaker started Model Y production at Gigafactory Shanghai in December 2020. The table below illustrates annual production capacities…
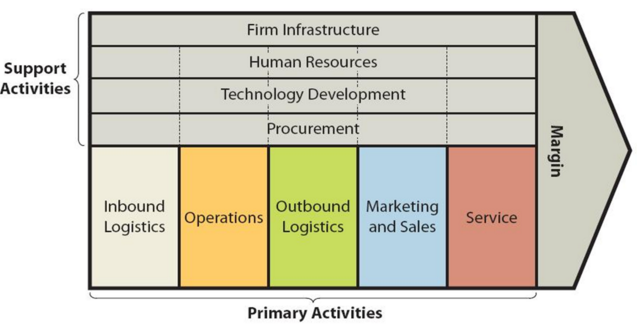
W.W. Grainger value chain analysis is an analytical framework that assists in identifying business activities that can create value and competitive advantage for global MRO products distributor. Figure below illustrates the essence of Grainger value chain analysis. W.W. Grainger Value chain analysis Grainger Primary Activities Grainger Inbound logistics Grainger inbound logistics involves receiving and storing MRO products by the global industrial supply company in its distribution centres for subsequent shipment to customers. The worldwide distributor of industrial products purchases approximately 1,7 million types of MRO products from approximately 5000 suppliers worldwide and stores them in distribution centres. Economies of scale is a major source of value creation in inbound logistics for the global industrial supply company. Additionally, the B2B distributor benefits from its strategic relationships with its suppliers in general and key suppliers in particular. Grainger Operations Grainger operations are divided into the following three segments: 1. United States segment. This segment generated sales of USD 8,6 billion in 2018, 72% of total revenue of the company.[1] The industrial supply company divides its customers in US segment into two categories according to complexity of their needs. a) Large customers in the US. Customers in this segment have complex needs and require services at their place of business. Grainger source of value creation in dealing with large customers in the US include adoption of partnership approach and assisting customers to reduce total cost of ownership in MRO spend by helping them to manage their labour, product and inventory costs. b) Medium customers in the US. This customer segment has less complex needs compared to large customers. Moreover, medium or mid-size customers in the US are mainly concerned with the solutions of their immediate business problems. Ranges and prices of products can be specified as major source of value creation…
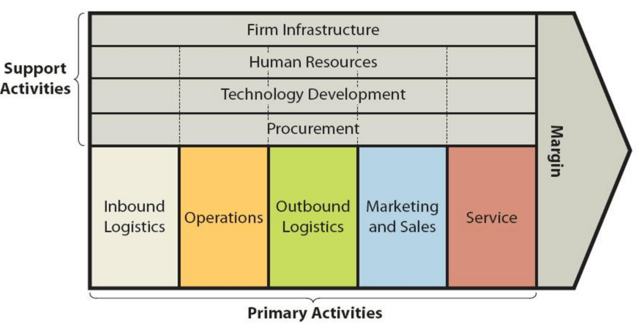
Airbnb value chain analysis is an analytical framework that assists in identifying business activities that can create value and competitive advantage to the global rental and experiences platform. Figure below illustrates the essence of Airbnb value chain analysis. Airbnb Value Chain Analysis Primary Activities in Airbnb Value Chain Analysis Airbnb Inbound logistics In traditional businesses inbound logistics involve receiving and storing raw materials to be used to manufacture products. Inbound logistics is different in service industry in general and online service in particular due to differences between products and services that include inseparability, intangibility, perishability and heterogeneity. From this perspective, Airbnb inbound logistics can be divided into two groups: 1. Inbound logistics related to core services. Core services for the company comprise peer-to-peer listings of accommodation, experiences and adventures. Airbnb inbound logistics for its core services takes a few minutes thanks to purely online nature of its business. Specifically, hosts can list their properties or experience services on the website of the lodging colossus on a matter of a few minutes. Therefore, inbound logistics of each new addition to its website comes for no extra cost for Airbnb. 2. Inbound logistics of resources and items that are used to aid the facilitation of core services. The global hospitality service brokerage company also uses a range of physical resources such as stationary items for its offices. Moreover, products like pillows and mugs, distributed to hosts occasionally to motivate them can also be mentioned as resources acquired by the travel industry disruptor to aid the facilitation of core services. Economies of scale can be specified as the main source of value addition in Airbnb inbound logistics of items that aid in facilitation of core services. Airbnb Operations Generally, operations involve the transformation of raw materials into finished products in manufacturing…
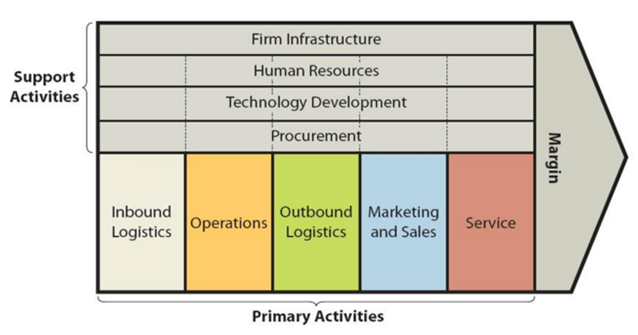
Microsoft value chain analysis is an analytical framework that assists in identifying business activities that can create value and competitive advantage to the business. Figure 1 below illustrates the essence of Microsoft value chain analysis. Figure 1 Microsoft Value Chain Analysis Microsoft Primary Activities Microsoft Inbound logistics Microsoft contracts with multiple suppliers internationally, as illustrated in Figure 2 below. Accordingly, the company has to maintain highly complicated supply-chain operations without any disruptions. It is compulsory of all suppliers to adhere to Microsoft Supplier Code of Conduct and The Microsoft Supplier Requirements. The main sources of value for Microsoft inbound logistics include the economies of scale, presence of strategic relationships with suppliers and in-depth knowledge of supply-chain management practices due to selling relevant software i.e. Microsoft Dynamics AX. Figure 2 Microsoft production supplier locations[1] Microsoft Operations Microsoft Corporation business is divided into the following three operating segments: 1. Productivity and Business Processes. This segment comprises Microsoft products and services related to productivity, communication, and information services. The segment comprises a range of devices and platforms such as Office Commercial, Office Consumer LinkedIn and Dynamics. 2. Intelligent Cloud. This operating segment includes public, private, and hybrid server products and cloud services that can power modern business. Intelligent Cloud segment comprises server products such as SQL Server, Windows Server, Visual Studio, System Center, and related CALs, and Azure, as well as, Enterprise Services, such as Support Services and Microsoft Consulting Services. 3. More Personal Computing. This segment consists of products and services geared towards harmonizing the interests of end users, developers, and IT professionals across screens of all sizes. Microsoft’s regional centre in Ireland supports the European, Middle Eastern, and African region; the centre in Singapore supports the Japan, India, Greater China, and Asia-Pacific region; and the centres in Fargo, North…

Xiaomi value chain analysis is an analytical framework that assists in identifying business activities that can create value and competitive advantage to the mobile internet company. Figure below illustrates the essence of Xiaomi value chain analysis. Xiaomi Value Chain Analysis Xiaomi Primary Activities Xiaomi Inbound logistics Xiaomi inbound logistics involves the delivery and storage activities of raw materials by the mobile internet company. Strategic relationships with Taiwan-based manufacturers of various components is one of the main sources of value for Xiaomi inbound logistics. Specifically, Xiaomi partners with Inventec and Hon Hai for assembly, Wintek and TPK for screen technology and Unicorn for PCB (printed circuit boards). Moreover, Taiwan Semiconductor Manufacturing Corporation (TSMC) is the main processor supplier for the company. Xiaomi also procures various electronic components from nearby countries. For example, MOS and batteries are mainly imported from Thailand. Xiaomi Operations Operations activities within Xiaomi value chain analysis refer to the processes of transforming raw materials into ready products. The mobile internet company has established its presence in 70 countries and regions and it is among the top 5 in 16 markets. Xiaomi manufactures locally more than 75% of smartphones it sells in India.[1] Location of manufacturing units in China and India is one of the main sources of value in Xiaomi operations. This is because the costs of human resources in these developoing countries are cheap. Along with proximity of manufacturing units to the sources of raw materials, cost-effective human resources play an instrumental role in sustaining cost advantage competitive edge of the business. Moreover, Xiaomi sophisticates its manufacturing processes in a systematic manner using advanced technologies and benefiting from technological innovations. Xiaomi Outbound Logistics Initially, Xiaomi outbound logistics practices were limited to the shipment of products directly to end-users via couriers. At that stage the company…
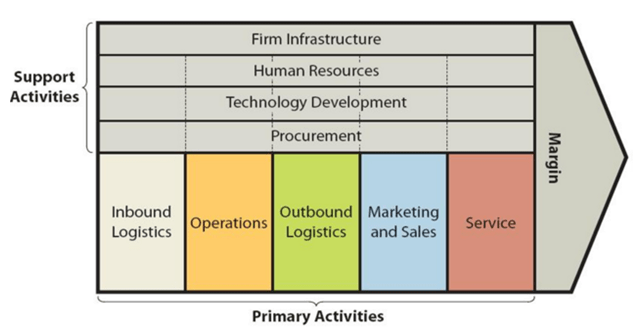
Samsung value-chain analysis is an analytical framework that assists in identifying business activities that can create value and competitive advantage for the global electronics company. Figure 1 below illustrates the essence of value chain analysis. Figure 1 Samsung Value chain analysis Samsung Primary Activities Samsung Inbound logistics Samsung has 579 suppliers globally and the company’s supply chain includes over 2,700 suppliers in various industries across the world.[1] The majority of Samsung suppliers are based in Asia and accordingly, 79.4% of its supply-chain expenses occur in Asia. This is followed by Americas (14.8%), Europe (4.4%) and other places.[2] In order control inbound logistics aspect of the business more effectively, Samsung owns a number of logistics firms as its subsidiaries. The most notably, Samsung Electronics Logitec, established in 1998, is an integrated enterprise logistics management agent that serves logistics needs of the company with 540 employees and 8,600 partner employees around the globe.[3] Figure 2 Samsung supply chain management principles[4] Strategic relationships with suppliers is one of the main sources of value creation for the multinational electronics company. For example, the company changed the payment cycle from twice a month to four times a month in 2011 and implemented early payments around Korea’s traditional holiday seasons, thereby helping to smooth the funding of operations for suppliers.[5] Samsung Operations Samsung Electronics is a global company that operates 38 production bases in 17 countries around the world.[6] The company manufactures 90% of its products in-house. Samsung operations are divided into three key divisions: IT & Mobile Communications (IM) Consumer Electronics (CE) Device Solutions (DS) At the end of 2015, Samsung Electronics maintained 199 worldwide operation hubs, including manufacturing subsidiaries, sales subsidiaries, design centres, research centres, and 15 regional head offices worldwide. Figure 3 below illustrates the full scope of Samsung global network of operations.…
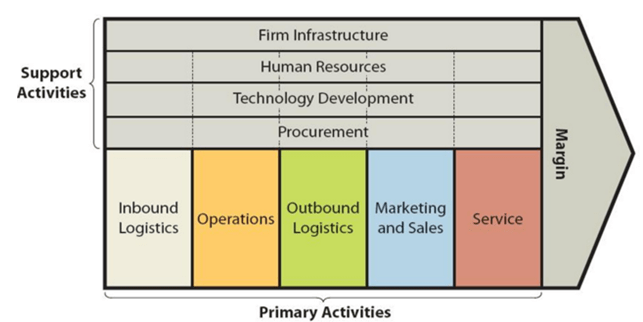
Google value-chain analysis is an analytical framework that assists in identifying business activities that can create value and competitive advantage to the business. Figure 1 below illustrates the essence of Google value chain analysis. Figure 1 Google value chain analysis Google Primary Activities Google Inbound logistics It can be argued that Google generates the greatest value in inbound logistics activities compared to other activities. Google’s core business is search. Internet users use Google’s search to find information they need, therefore the list of content generated as search results can be specified as ‘product’ provided by Google. The content Google generates as search result is created by private and organizational internet users and it comes to Google free of charge. Therefore, due to unique aspects of Google’s business model there is no inbound logistics costs for its core search business. Google also uses an extensive range of hardware, technological equipments and tools to conduct its business operations. The internet giant does not reveal the details of its supply-chain management and inbound logistics to the public. Google maintains a dedicated supplier site, where suppliers can submit invoice for payment, check invoice status and deal with a range of other administrative aspects of their cooperation with the company in a convenient manner. Google Operations Google operates via more than 70 offices in more than 40 countries internationally. Google offices are famous for their creative design and the presence of distinctive features such as sharing cubes, video games, pool tables, pianos, cafes and others. Google headquarters in Mountain View, California consists of about 4.8 million square feet of office and building space, along with about 15 acres of land that can be ground for more office space in the future. The major source of value in Google’s operations can be specified as the company’s…
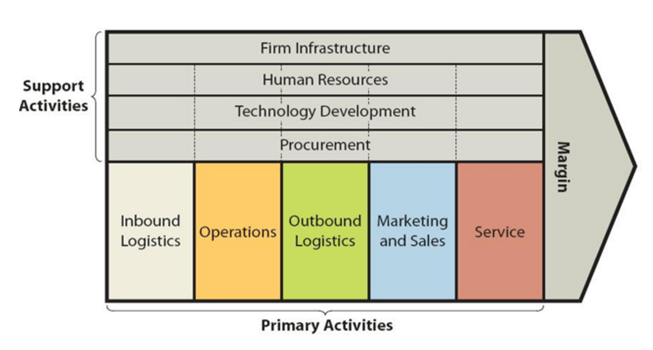
Value chain analysis is a strategic analytical tool that can be applied to analyse business activities to be able to identify those activities that contribute most the overall competitive advantage of the business. Facebook value chain analysis provided below discusses sources of competitive advantage of the social media company by referring to its primary and support business activities. Figure 1 below illustrates the essence of value chain analysis. Figure 1 Facebook Value Chain Analysis Primary Activities Inbound logistics Facebook Inc. inbound logistics refers to ways the company acquires resources and uses according to its needs. The range of resources used by the social media giant includes hardware, various types of technologies and office supplies. Generally, value chain analysis framework analyses the processes of receiving and storing raw materials until their transformation into the final goods. However, due to Facebook Inc.’s business model illustrated in Figure 6 below, tangible resources such as hardware and technology used by the company are only secondary in their nature and the primary resources used to attract the customers are intangible. Specifically, Facebook offers its customers unique intangible ‘products’ of informational nature, i.e. content. From this point of view, inbound logistics of content is highly cost-effective since the content is uploaded by users of in the forms of texts, pictures and videos without any additional costs for the business. Operations Facebook is available in more than 90 different languages, and the company has offices or data centres in more than 30 countries around the world. Moreover, there are five support offices and more than 35 sales offices located globally.[1] Approximately 84.5% of Facebook daily active users are outside the US and Canada.[2] As it is illustrated in Figure 2 below, Facebook operations mainly involve the transformation of raw content into user-friendly format via profile page, timeline,…